MicroCORE®
The MicroCORE® technology is a unique patented offering from DIAMANT.
Increase your cuttings recovery and collect small sized cores while drilling to unlock your formation evaluation with our patented MicroCORE® technology. And increase your ROP along the way !
The MicroCORE® technology bits from DIAMANT generate a small diameter uncut formation (MicroCORE) in the center. As the uncut formation is long enough to touch the base of the bit body, the angled base in the center forces the uncut formation to brake off by design then the generated MicroCORE is ejected into the annulus through the opening in between the blades.
Diameter and length of MicroCORE generated by the MicroCORE® technology bits are optimized considering following critical aspects:
- Size of the hole being drilled.
- Clearance between hole and BHA
- Rate of Penetration
- Rig Hydraulics
Considering above listed factors, the DIAMANT team can design and offer a MicroCORE® product specific to your operations to generate good quality of formation samples for reliable geologicial studies.
StormEYE®
No cutting action in the center of a PDC bit can improve your ROP up to 30%, more so in hard and compacted rock. Our Unique and patented StormEYE® combines the MicroCORE® technology and shaped cutters strategically placed on cutting structure to increase your ROP potentials even higher.
By optimizing energy distribution on cutting structure with no cutting action in the center, the StormEYE® technology delivers more energy to the cutters that fail formation thereby maximizing the rate of penetration (ROP) potentials up to 30% over conventional PDC bits.
In addition to the benefits of the patented MicroCORE® technology, the superior penetration efficiency of “Scribe” shaped cutters enables the StormEYE® technology pushes the envelope of energy savings in the center even further to fail the formation for optimum bit performance.
The StormEYE® design uses scribes shaped cutters in two distinctive locations: the first is the inner cone where wear is never critical (lower linear speed) but normal forces consumption higher. The second use is scattered on the rest of the cutting structure in a way where full round cutters are trailing scribe cutters that initiate the cut with optimum energy.
Contact your local DIAMANT representative for more details on the StormEYE® technology.
KATANA™
Body material is an essential component of any bit as it holds the cutting structure in place and sustain the stress resulting from the cutting process.
There are two main body materials considered in drill bits:
- Steel
- Matrix (Infiltrated tungsten carbide)
When Matrix is usually preferred in though & abrasive environments; Steel is the common solution in soft & sticky formations.
The Katana™ technology is a multi-material solution that allies the resilience & manufacturing advantages of Steel to the toughness and abrasion resistance of Matrix
The Katana™ Bit Technology is based on the Katana sword which consist of a core of softer steel encapsulated in a hard-laminated structure. These swords are known for their relentless resilience.
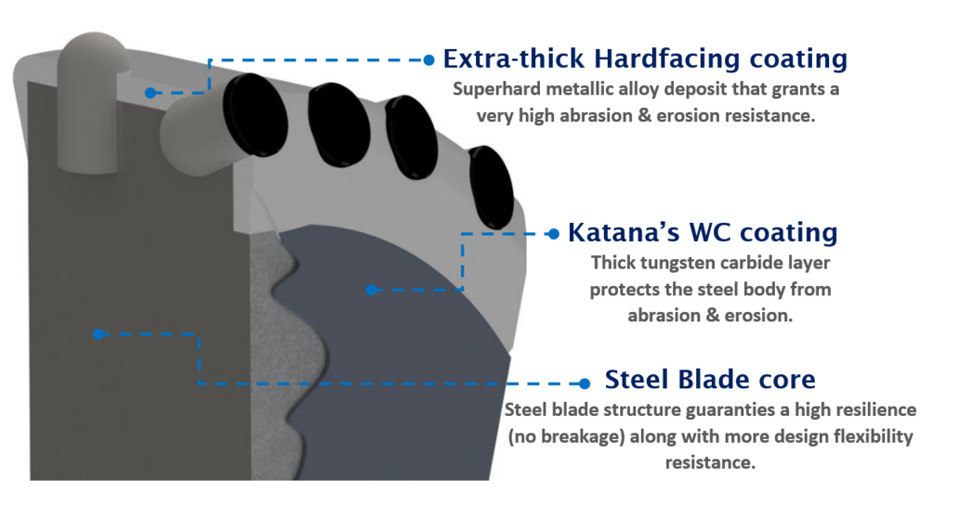
WARTHOG™ Cutting Layout
DIAMANT has developed the WARTHOG™ cutting layout (W) to optimize PDC bit performances in challenging applications where lithology is very interbedded or BHA poorly stabilized (or slick) and when axial vibration cannot be avoided.
Engineered around 3 key principles (cutter protection, bit torque response & tool face control), the WARTHOG™ unique layout is set with 2 independent rows of shock reducers per blade to maximize the protection of the PDC cutters (increasing the contact surface in case of shock) and prevent premature breakage of chipped diamond table.
The PDC cutting layout itself is engineered in a way to optimize reactive torque generated by bits to help limit vibration the BHA's vibrational tendencies and improve tool-face control.
Field results has proven that the WARTHOG™ layout reduces premature cutter breakages and chippage by 50% compared to PDC bits offering conventional layouts without sacrificing the penetration rate potentials.

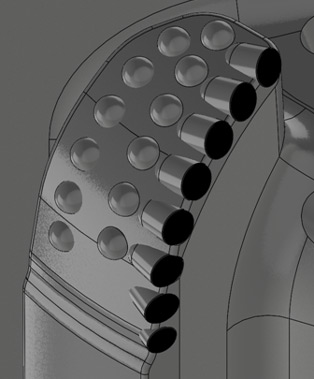
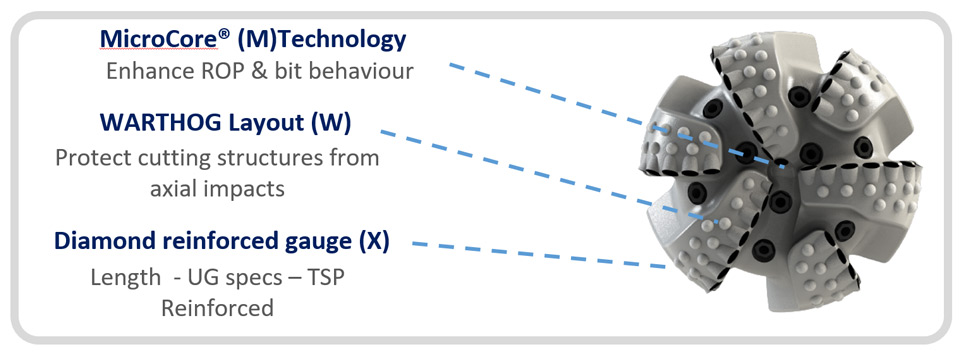
PEXUS™
We offer PEXUS™ Hybrid bits from Shear Bits through a license agreement in place between both companies.
PEXUS™ technology combines the "gouging" cutting action provided by Roller Cone bits and "shearing" cutting action provided by PDC bits into one product.
PEXUS™ products are developed to address the weaknesses of conventional products. The result is a drill bit technology that increases the penetration rates while mitigating the risk of premature failures.
PEXUS™ technology enables the operators to effectively drill through formations that are commonly accepted as destructive to PDC cutters (i.e. conglomerates, chert, pyrite).
Size range offered are from 3-7/8” to 24” with application specific blade counts and cutter sizes.